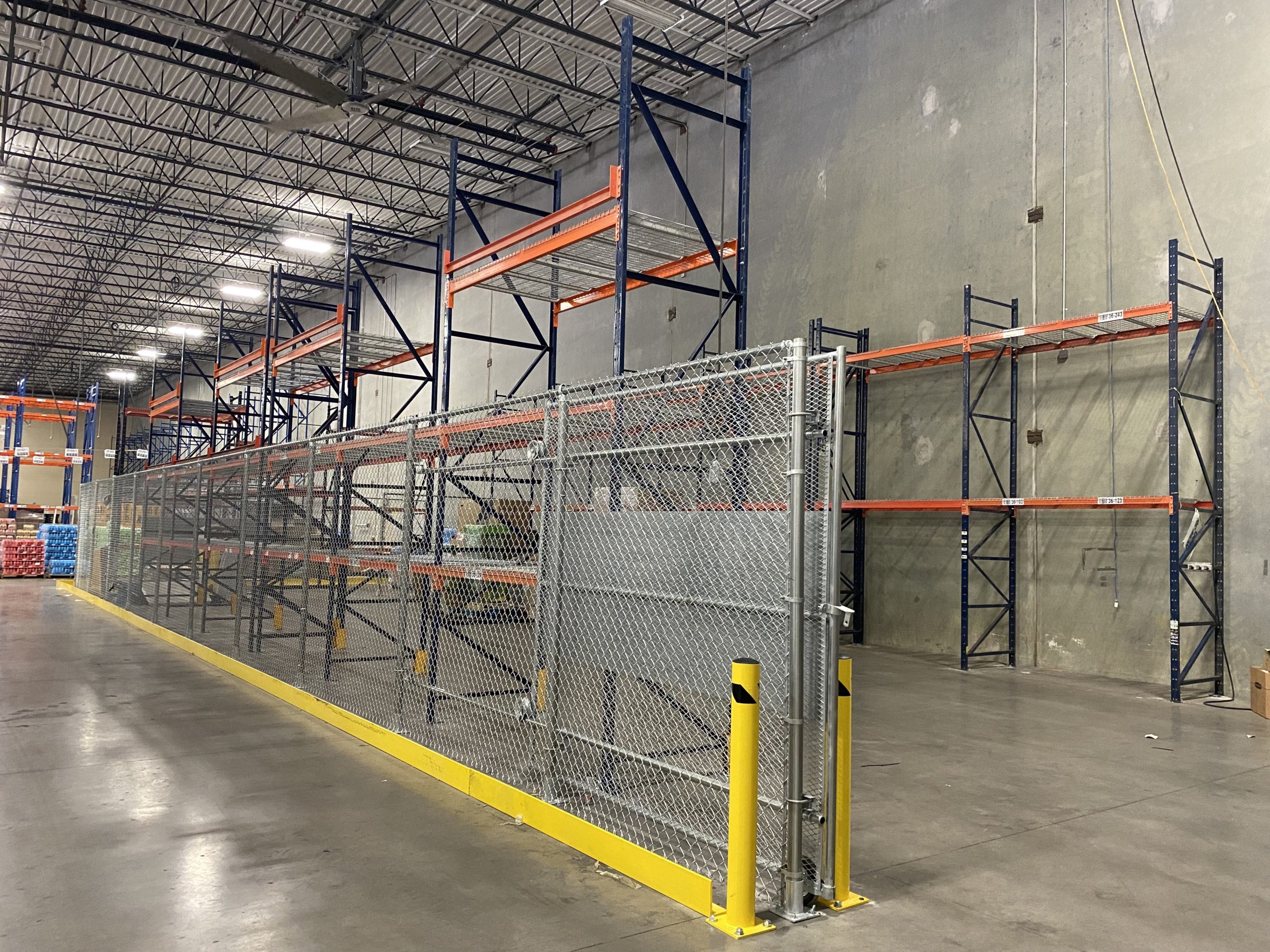
Industrial Fencing
Industrial fencing has a variety of purposes. It is often used to protect high-value items, manage hazardous materials, or to delineate operational areas in a facility.
Efficient Storage Solutions can:
Design, procure, and install new chain link or wire mesh fencing. Furthermore, we can relocate your existing fencing and add gates or additional lineal feet as required.